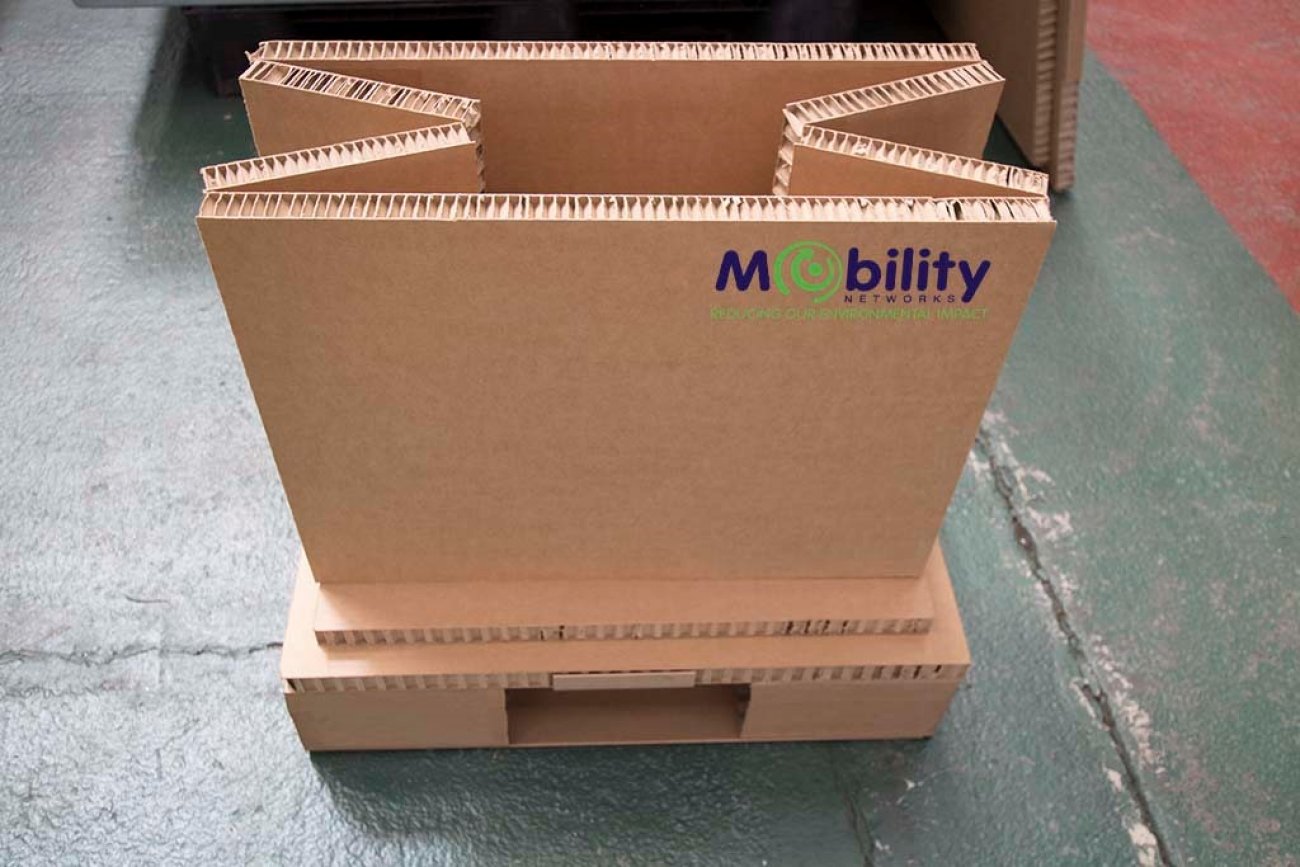
Shipping products from one of its factories, PLS in the UK, to customers all over the world, Mobility Networks is determined to continue reducing its environmental impact, by using a more sustainable and revolutionary packaging process.
Used as an alternative to wood (26kg average weight) and plastic (average weight of 30kg), the new purpose-built cardboard pallets and boxes are engineered with honeycomb technology and weigh as little as 6.5kg!
This new method of packaging allows us to significantly reduce fuel consumption and carbon emissions with one hundred per cent recyclable cardboard materials.
Shipping products abroad has also become effortless as the new packaging is exempt from ISPM 15, an international standard developed by the International Plant Protection Convention (IPPC) to address the need to treat wood materials of a thickness greater than 6mm, used to ship products between countries.
Other benefits include better manual handling due to its minimal weight and the substantial reduction of workplace injury as there are no nails or splinters on these innovative boxes and pallets.
The initiative of finding a cutting-edge packaging alternative to traditional methods is part of Mobility Networks’ Lean System of continuous improvement in all pre-and post manufacturing process, aligned with the brand values of Agility, Expertise, Leadership and Cost-efficiency.
Shipping products all over the world, the new packaging is part of the Lean continuous improvement system.
The new packaging system by Mobility Networks reduces manual handling and work related injuries as it does not have nails and splinters.
Traditional packaging such as wooden boxes and pallets require ISPM 15 treatment when used to export products (exempt with the new packaging system used by Mobility Networks).